Suite de l'étude précédente :
Maintenant qu'on dispose du kit complet, on va pouvoir passer à l'action !
Très occupé en ce moment j'écris ce billet bien tardivement, de mémoire et depuis mes quelques notes… Pas l'idéal pour la rigourosité des informations écrite ci-après, mais cependant utile pour un certain recul laissant de côté les écueils afin d'aller directement à ce qui fonctionne.
La boite :
- Suivant les plans réalisé en 3D avec Sketchup j'ai procédé à la découpe des planches de medium de 10 mm l'épaisseur.
Il faut deux côtés : 45,5 × 32 cm.
Le fond : 36,4 × 34 cm.
Et le dessous : 36,5 × 32 cm.
Une planche supplémentaire en bois de récupération est utilisée pour former le second dessous plus épais.
- D'abord reporter toutes les dimensions sur le « bois ».
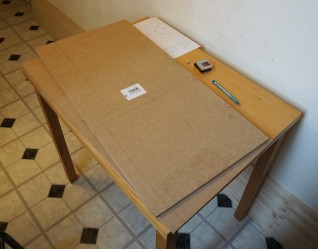
- J'utilise la technique de la règle pour découper des traits droit à la scie sauteuse.
Il suffit de reporter la distance de la lame en tenant compte de son épaisseur (avec ma scie c'est 3,25 cm) et de découper en suivant la règle avec, chose très importante, une lame à chantourner !
Cette lame à la capacité à changer de direction pour faire des arrondis grâce à ses dents orientés dans deux directions.
Et là tu te dis, « mais wtf, on va tout droit ! », et moi je te dit, justement !
Une lame classique, avec ses dents alignées vers l'avant uniquement aura tendance à se décaler vers le côté opposé à l’appuie de la scie contre la règle, sorte de contre réaction due à la contrainte, même légère sur la souplesse de la lame.
Et là bah t'es comme un gland car comme dans un rail, la lame est entraînée en dehors du trait de coupe et c'est impossible à rattraper…
Alors qu'une lame à chantourner se redressera d'elle même car elle coupe devant et aussi sur ses deux côtés ^^
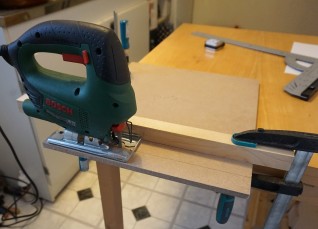
- Voila un assemblage à blanc.
Il est important de faire un montage le plus orthogonal possible, faut vraiment pas hésiter à y passer du temps en multiple vérifications avec une bonne équerre.
J'ai utilisé des vis à bois assez fine mais longue (Ø3 mm × 30 mm, car Je rappelle, l'épaisseur du « bois » n'est que de 10 mm.
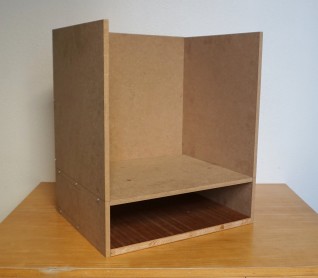